Laboratory of structural aluminium alloys
Since 1955 the Institute have been developing high-strength
aluminium alloys for marine applications. Demand for these alloys arose in connexion with need for creation of high-speed fleet and dynamically-supported ships – hydrofoil and air-cushion ships.
As aluminium alloys used for sea-going ships shall have high corrosion resistance and good weldability the aircraft-grade aluminum developed specially for riveted (not welded) aircraft structures with low corrosion resistance in sea water was not suited to shipbuilding. Institute developed aluminum-magnesium alloys of new class with high corrosion resistance in sea water and good weldability using all types of welding. To increase strength and corrosion characteristics of weld joints from these alloys no additional heat treatment is required – their strength and corrosion resistance practically do not differ from similar properties of initial material.
The aluminium-magnesium alloy of the 1561 grade is the most promising; due to its optimal chemical composition and original technology a structure ensuring a set of characteristics significantly exceeding parameters of similar foreign alloys was created. The 1561 alloy at annealed and hot-rolled state has yield strength not less than 180 – 210 MPa (depending on type of semi-finished product), ultimate strength not less than 340 MPa and strength of welded joints not less than 0.9 of strength of base material. For more than 40 years the 1561 alloy is the main structural material for manufacturing of welded hulls of home-produced high-speed hydrofoil and air-cushion ships.
Thanks to large-scale implementation of the 1561 alloy about 1000 hydrofoil and air-cushion ships such as Kometa, Polesie, Voskhod, Kolkhida, Irbis, Gepard, Linda ships and others with passenger-carrying capacity from 30 to 300 persons were built. The Lun, the world’s largest airfoil boat with passenger-carrying capacity of 150 persons was build from the 1561 alloy.
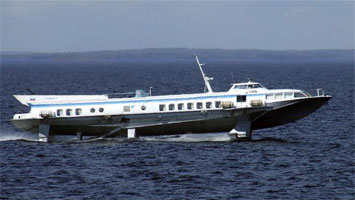 |
|
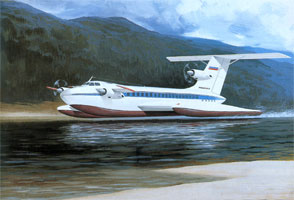 |
Hydrofoil and air-cushion ship of the Kometa type |
|
Project of the passenger airfoil boat |
The 1561N alloy with yield strength and ultimate strength of 250 MPa and 360 MPa correspondingly was developed based on the 1561 alloy.
In 90s of the 20th century in order to increase strength of aluminium-magnesium alloys the Institute developed a high-strength non-heat-treatable alloy additionally alloyed with scandium of the 1575 grade. Alloy has an unique high strength for alloys of this system (yield strength and ultimate strength are not less than 300 MPa and 400 MPa correspondingly) keeping a high corrosion resistance and weldability.
Main advantage of the 1561 and 1575 alloys is the following: they are well welded by means of all fusion welding types, at the same time the hardening heat treatment of welded joints is not required as welded joints of these alloys have strength and corrosion resistance at the level of properties of base metal without additional heat treatment. The 1561, 1561N and 1575 alloys are irreplaceable in building of large-sized light welded structures which shall have high strength, corrosion resistance, reliability and repairability in service.
In some cases new possibilities of use of alloy with scandium are found, for example combination of high-temperature ductility with increased strength within the range of operating temperatures or advantages of this alloy for operation at cryogenic temperatures. Aluminium alloys developed by Institute may compete with titanium alloys at cryogenic temperatures taking into account their lower costs, lower specific gravity and lower tendency to hydrogen brittleness.
Production of all semi-finished products required for shipbuilding from the 1561, 1561N and 1575 alloys was mastered. Molded panels representing constructional elements consisting of plates with thickness of 3-16 mm, width up to 2000 mm and length up to 9.0 meters with longitudinal ribs of different sections have a special place. Production of more than 30 standard sizes of shipbuilding-purpose panels were mastered at Samara iron and steel works.
Use of such panels in national shipbuilding increased productive efficiency of assembly and welding works in 2.5-3.0 times; reduced working hours for manufacturing of 1 t of hull structures by 400 labour hours; increased bearing capacity, reliability and quality of hull due to reduction of amount of welded joints.
Weight of panels used in building of high-speed ships achieves 60 and more percents of the hull weight.
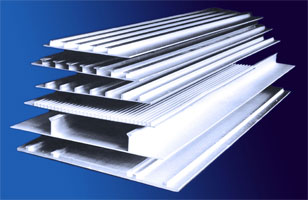
Panels from aluminium alloys for high-speed ships
With development of marine facilities and creation of new class of ships for example airfoil boats a demand arose for structural high strength materials. Institute developed a series of high-strength corrosion-resistant heat treated alloys of the Al-Zn-Mg system with yield strength of 280-350 MPa and aluminium-based laminated composite materials.
The 1980Т1 heat hardenable alloy of the Al-Zn-Mg system has high strength (yield strength not less than 300 MPa), high corrosion resistance in sea water and satisfactory weldability. To increase strength and corrosion resistance of welded joints made from this alloy special low-temperature modes of heat treatment were developed. Production of rolled sheets and plates, extruded pipes, bars, sections and forgings from the 1980Т1 alloy was mastered. Use of this alloy for shell and framing of ship hulls, tanks for special medium, drilling pipes and tubing, parts manufactured from castings and forgings for operation at temperatures up to (+100)0С, search, rescue and research deep-sea vehicles is promising.
The further works on increase of strength of heat hardenable alloys resulted in creation of alloys of the 1941 and 1943 grades of the Al-Zn-Mg-Cu system which have high strength characteristics: ultimate strength of 440-460 MPa, yield strength not less than 350-400 MPa, good manufacturability and high corrosion resistance in sea water. Alloys are recommended for manufacturing of critical loaded not-welded structures operated under sea conditions within the range of temperatures from - 40 to 1000С.
Production of sheets with thickness of 1-10 mm, extruded sections of different configuration and sizes and extruded pipes was mastered and they are launched into serial production. Drilling pipes made from the 1941 alloy were operated in drilling of the Volga region oil wells. Use of drilling pipes made from high-strength corrosion-resistant aluminum alloys is very promising as it allows to increase drilling speed and well depth due to weight-saving of drill stems.
High corrosion resistance of aluminium alloys significantly exceeding corrosion resistance of structural steel allows to increase service life of gas and oil-production equipment operated in aggressive medium (hydrocarbons, oilfield brine containing chlorides, sulfates, organic acids, carbon dioxide); therefore their use in production of pipes and parts of drilling units, tanks for storage and transportation of oil is very promising.
Developed aluminium alloys are suited to use in structures designed for operation in the Arctic region. Aluminium alloys as metals with face-centered cubic latitude are not only subjected to low-temperature embrittlement but have an increased (by 20%) strength and ductility with decrease of temperature to (-196)0С.
Prediction developments performed by CRISM "Prometey" on foreign and home-produced aluminium alloys for liquefied gas storage and transport containers showed that the 1561 and 1550 alloys have not a tendency to embrittlement at cryogenic temperatures up to (-196)0С; at that their strength and ductility monotonely increase with reduction of temperature. Results of comparative tests performed under static and dynamic loading showed that properties of home-produced aluminium-magnesium alloys are similar with those of the 5083 foreign alloy which is allowed to be used for construction of gas carriers according to Lloyd standards.
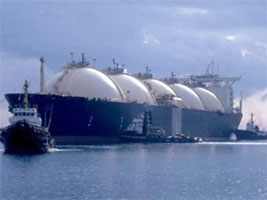
Gas carriers
Shipbuilding-purpose high-strength corrosion-resistant aluminium-magnesium alloys with guaranteed yield strength ≥ 180 MPa developed by Institute are promising for use in structures of gas carriers.
Bimetal aluminium-steel
Aluminium-based laminated composite materials
Process of development of national and foreign shipbuilding shows that aluminium alloys are becoming more common in building of sea and river ships with steel hulls; they ensure total weigh reduction, center-of-gravity reduction and other advantages. lightness, non-magnetization, corrosion resistance and enough high strength. Deck erections, deck houses, bridges, chimney casings, compartments, enclosures etc. were manufactured from aluminium alloys.
Joining of aluminium and steel structures may be performed by riveting or welding using bi-meal adapters. As practice of ship running shows a riveted assembly if not enough reliable and long-life. In manufacturing of structure construction from heterogeneous materials (particularly of steel and aluminium) their joining using be-metal is the most advanced method. In this case homogeneous materials are welded through a bi-metal adapter. Replacement of riveted joints for welded ones resulted in reduction of labour intensity of structure manufacturing, increase of service life and corrosion resistance.
Foreign shipbuilding and ship repair widely use bi-metal material based on low-alloy steel and aluminum-magnesium alloy with thickness of 37-40 mm made by means of explosion welding with layer adhesive strength in tear-resistance test not less than 70 MPa.
In order to increase corrosion resistance of welded steel-aluminum joints and to avoid use of difficult-to-obtain and expensive nickel-based materials the Institute developed a technology and mastered at the Research and Experimental Complex production facilities the low-tonnage production of new shipbuilding bi-metal material of the KBM-1 grade based on low-alloy steel of the 10KhSND grade and aluminium alloy of the 1561 grade. Material is a composition of aluminium alloy and steel manufactured by joint rolling with one-component deformation of aluminium layer with symmetrical (conventional) and asymmetrical (commingled) layer arrangement. It is produced in the form of strips with thickness of 8-12 mm, width up to 130 mm and length up to 2000 mm. Adhesive tear strength of bi-meal layers is not less than 100 MPa, shear strength is not less than 55 MPa.
Low-tonnage production of the KBM-1 bimeal strips by CRISM "Prometey" is witnessed in the system of Russian Maritime Register of Shipping.
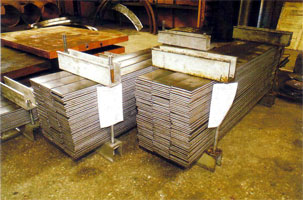
Bimeal strips. Batch of the KBM-1 bimeal based on low-alloy steel of the 10KhSND grade
and aluminium alloy of the 1561 grade
Institute developed a technology of welding of steel-aluminum joints using the KBM-1 bi-meal and elaborated a required technical standard documentation. Based on these developments the bi-metal is recommended by the Russian Maritime Register of Shipping for fusion welding of aluminium deck erections with steel hull of ships of all classes and purposes. Bi-metal may be successfully used in manufacturing of steel-aluminum welded structures of different classes and purposes.