Research and production complex
"Structural steels and functional materials for marine
facilities"
Alexey
V.
Ilyin
Deputy director general for research work,
Head of Research & Production Complex "Structural
steels and functional materials for marine facilities",
Doctor of Technical Sciences, Docent
Research and production complex profile:
- development of high strength, cold-resistant, corrosion resistant and nanostructured steels with unique level of useful quality;
- development of metallurgical processes of semifinished material manufacturing including shaped sections and sheet products, castings and forgings;
- creation of welding materials and development of technologies and processes of manual welding, semiautomatic gas-shielded welding, automatic gas-shielded welding and flux welding, multiarc welding, electron beam welding and laser welding;
- development of technologies of copper alloy welding and welding deposits in homonymous and heteronymous combinations;
- research and development of new structural and functional nanomaterials and coatings with amorphous, microcrystalline, nanophase, intermetallic structures, manufacturing and production processes;
- works on creation of original nanomaterials, development of structural and functional elements and products made on their basis, application of functional coatings;
- performance study of basic material and weld joints with determination of safe operation resource, design and technological and local strength of weld joints and structures, monitoring and forecasting of material and welded structure service life;
- study of composition, structure, physical and mechanical properties of materials;
- operational NDT inspection of material structure and properties;
- corrosion and corrosion and mechanical tests of structural materials;
- metrological services and certification of structural materials.
First home-produced high-strength hull plates and technologies of their manufacturing were developed by Institute in the middle of 20th century when a demand for development of steels having both good weldability and high brittle fracture resistance, significantly higher fatigue resistance and corrosion and mechanical resistance arose.
Drastic improvement of processing and physical and mechanical properties of steel was reached in the early 1970's after development and implementation of electroslag remelting technology as a result of which a series of new hull plates with significantly higher strength was created.
Over the last years production of such hull plates was organized at PАО Severstal, OMZ-Special Steels LLC, MMK Group using fundamentally new energy-efficient technology. Institute work on re-creation of hull plates in Russian Federation was honored with Russian Federation Government prize for 2011.
In parallel with development of electroslag remelting technology of high-strength hull plates the Institute created a series of the AB steels. New steels are distinguished by increased cold resistance and weldability that allows to use them extensively in different industries from shipbuilding to crane manufacturing. Taimyr, Vaigach, 50 Years of Victory icebreakers, atomic lighter-carrier ships, high-speed train wagons etc. were built using these steels.
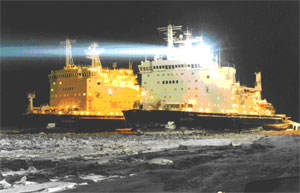 |
|
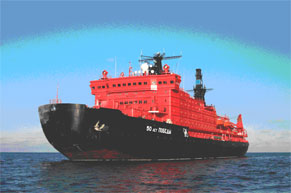 |
Vaigach icebreaker |
|
50 years of Victory icebreaker |
Production technology of the AB steels using secondary metallurgy processing was developed in 1995-1998. The AB steels developed based on modern achievements of metal science and metallurgy due to formation of dispersed through-thickness uniform bainitic-martensitic structure provide the following:
- high resistance to brittle fracture particularly under conditions of jumping temperatures from - 50 to +100 °С;
- resistance to laminated damages in welded assemblies including under high tensile stresses in the direction of sheet thickness;
- high resistance to alternating loads causing fatigue fractures;
- good weldability allowing modular and sectional manufacturing of large-sized structures with the subsequent assembly at low temperatures outdoors.
- guaranteed resistance to corrosion and corrosion and mechanical damages.
These steels are successfully used for manufacturing of heavy loaded welded
structures operated at temperatures from -40 to +100 °С under conditions of
corrosion effect of sea water, repeated static and dynamic loading.
Primarily among these are ship hulls including for arctic vessels — atomic
lighter-carrier ships, icebreakers, tankers, gas carrier vessels, offshore
floating self-elevating and semi-submersible drilling rigs, unique
ice-resistant fixed platforms, deep-sea vehicles etc. Due to high level of
physical and mechanical properties, manufacturability and principally unique
weldability these steels can be successfully used in power-plant
engineering, construction of rolling stock for high-speed networks, crane
boats, pressure vessels etc.
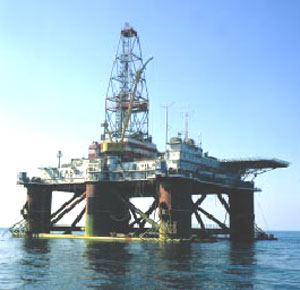
The Shelf floating semi-submersible drilling rig
Production of the AB steels is mastered at OMZ-Special Steels LLC, PАО Severstal, MMK Group.
Clad steels
Important achievement is a creation of stainless steel clad two- and three-layer composites based on the AB steels. Cladding technology developed by the Institute provides an absolutely reliable adhesion of basic and clad layers that allows to weld cruciform joints directly to clad layer without its removal.
Except for high resistance to standard corrosion these steels have exceptionally high resistance to corrosion and erosion wear in ice floes at low temperatures that allows to use them in ice linings of atomic icebreakers, drilling rigs and other facilities operated in the Arctic region. Certainly use of these steels in chemical industry, construction of storage and containers for toxic chemicals, radioactive waste etc, is also promising.
Research and production complex also developed new effective
welding materials and technologies of all listed steels: automatic submerged welding (ceramic and fused flux), mechanized gas-shielded welding with flux cored wire and manual coated electrode welding. They provide uniform strength of joint metal and base metal. Main feature of developed materials and technologies of their welding consists in high-quality welding without heating or in case of significant thickness of structures to be welded — with moderate heating.
Nitrogen steels
Institute achieved a great progress in development of nonmagnetic nitrogen-alloyed hull plates. The most dangerous corrosion – stress corrosion cracking in sea water – practically deleted a wide use of manganese-alloyed steels. Therefore the direction of development of nitrogen bearing austenitic steels was chosen as priority like the most effective and efficient. And really scientific, research and development works performed over the last years and their commercial run demonstrated the possibility of use of steel of this class in some civil and defence industries.
Cold resistance (up to minus 200оС) with a high strength is an unique property of nitrogen steels that allows to used them for construction of home-produced liquefied-gas carriers as well as liquefaction and liquefied gas storage stations. Use of these steels will allow to create an original national patentable structure of liquefied gas tanks as well as liquefied gas storage allowing to avoid purchase of foreign patents and licenses and ensure construction of gas carriers at Russian plants using existing facilities.
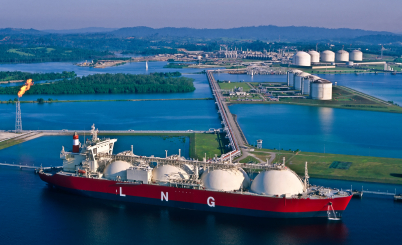
Liquefied gas tanker
Nitrogen steels are also interesting for development of drilling equipment for deep directional drilling.
High strength pipe steels and high performance technologies of the Х70-Х100
and К60-К70 large-diameter pipes manufacturing
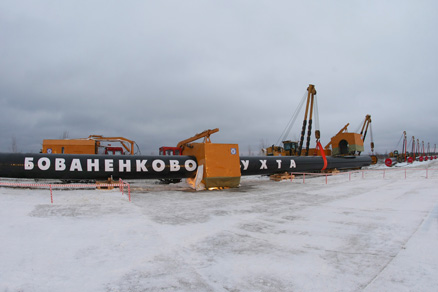
These pipes are developed for operation in north regions, they surpassed foreign equivalent steels as per results of field tests and competitiveness. Bovanenkovo-Ukhta gas pipeline was constructed using the Х70 pipes. This work makes possible a real use of pipes with strength category up to Х100 and К70 ensuring metal-saving, increase of oil and gas transportation volumes as well as provision of environmental safety for a period up to 40-50 years. Works at this direction are honored with Russian Federation Government prize for 2012.
Cold-resistant steels for the Arctic Region
Series of cost-efficient cold-resistant steels of different strength with several times increased properties was developed for marine facilities operated under extreme conditions of the Arctic Region; these steels showed good results in construction of the Prirazlomnoye and Arkticheskaya fixed and drilling platforms.
High competitiveness of developed steels caused by unique combination of lean alloying with level of strength, viscosity, cold resistance (up to -60°С), isotropy of properties, crack resistance and good weldability of sheet products provided a demand of steels in Russian and foreign markets.
Sheet products from cold-resistant steels are produced at CherMK OJCS Severstal, MMK Group, OMZ-Special Steels LLC, LDP - at ZAO Izhora Pipe Mill and ChelPipe. Necessary welding materials and technologies were developed for new steels.
New standard for delivery of shipbuilding steels including cold-resistant steels, GOST Р52927-2008 was developed.
Creation of new high-reliable materials with high level of useful quality for hydrocarbon production and transportation from the Arctic fields within the framework of the most important innovative Metal and Magistral projects of national standing in FSUE CRISM "Prometey" is a great breakthrough in development of Russian Federation industrial complex.
High strength steels of normalized composition
At the present time the Research and production complex is hard at work on development of energy-efficient and resource-saving production technologies of new improved materials – high strength steels of normalized composition. Experience obtained during important innovative projects of national standing, the Metal and the Magistral Projects, showed that actually existing variety of chemical composition can be reduced to several base compositions with minimum alloying and variety of industry requirements to physical and mechanical properties can be provided due to effective and low-cost production technology controlled based on mathematical modeling ensuring a required degree of nanostructuring.
Therefore development of material science in this direction will allow to solve the problems of construction of defense and peace-time industries not due to alloying of materials with expensive alloying elements but due to controlled technology of nanostructuring. At that at the same time a task of fundamental change in large-scale metallurgy can be solved. It is known that a big production of metallic materials using traditional methods of primary steelmaking in blast furnaces, basic oxygen furnaces, open-hearth furnaces, electric furnaces and especially production of alloying elements – chrome, nickel, molybdenum etc is very dangerous for environment and human. Standardization of chemical composition of steels, use of nanostructuring processes will allow to use to the full extent direct ore reduction processes, use of steel pellets, nodules etc. and other more environmentally friendly manufacturing methods.
At the present time development of structural nanomaterials is one of the most demand and at the same time the least understood domain of nanotechnologies.
By RF Government Decree No. 498 dtd. 02.03.2007 the Institute is classified as a leading organization of development of structural nanomaterials as part of national nanotechnological network within the framework of Federal Target Program "Nanoindustry infrastructure development in Russian Federation for 2007-2010". The Science and technology sector of development of structural nanomaterials (nanocenter) was created in Institute to solve set problems. Structure and equipment of Nanocenter with unique experimental, diagnostic, metrological, test and process equipment ensure the possibility to develop world-class structural metallic, nonmetallic and functional nanomaterials and coatings high-demanded almost in all industries.
Diagnostics and certification of materials
Examination of structure and properties of developed materials is performed on the base of the PROMTEST KM test laboratory of structural materials and in Scientific Equipment Common Use Center "Composition, structure and properties of functional and structural materials".
PROMTEST KM Test Laboratory is entered into State Register and accredited in Register of Shipping of Russian Federation and in the system of Federal Technical Regulation and Metrology Agency as a technically competent and independent test laboratory.
It is entitled to perform 144 types of mechanical tests of metallic materials using more than 1000 standards as well as any technical specifications and normative documents provided by customer.
The PROMTEST KM test laboratory meets requirements of GOST / ISO IEC 17025-2000 and GOST R 51000.4-96.
Supervisory control of the PROMTEST KM Test Laboratory activities is performed by Federal Technical Regulation and Metrology Agency.
Common Use Center (CUC) "Composition, structure and properties of structural
and functional materials"
CUC of CRISM "Prometey" was created in 2005 and forms part of the Institute.
CUC is intended for provision of service package and increase of efficiency of use of the Institute experimental and instrument base including physico-analytical measurement, test and process equipment and equipment used for a solution of problems defined by priority directions for development of science, methods and technologies of Russian Federation. CUC provides more than 200 types of different research works. CUC instrument base contains a fleet of new analytical equipment and intended for research works. CUC is equipped with more than 100 units of unique research equipment. CUC includes 13 laboratories providing scientific and technical services during tests.