Research and production complex
"Titanium alloys"
Valery P. Leonov
Deputy director general for research work
Head of Research & Production Complex "Titanium alloys"
Doctor of Technical Sciences
FSUE CRISM "Prometey" was the fist to initiate use of titanium alloys in hull shipbuilding. Institute created marine grade titanium alloys, technologies of industrial production, welding that allowed to develop a new subindustry of structural titanium alloys, to form a direction of high-strength marine grade titanium alloys that ensured construction of a series of deep-water facilities which have no comparable counterparts in the world. The following known scientists conducted pioneer research:
L.S. Moroz, I.V. Gorynin, I.V. Polin, B.B. Chechulin, S.S. Ushkov.
For over 60 years Research and Production Complex "Titanium alloys" performs studies in the field of development and creation of corrosion-resistant welding titanium alloys for structures used in shipbuilding, nuclear power engineering, chemical machine building and other industries.
Research and Production Complex "Titanium alloys" includes four laboratories which performed works to the following directions:
- Development of titanium alloys and technologies of their production for deep-water facilities, shipbuilding, offshore facilities and special products.
- Development of titanium alloy welding technologies and structural-and-technological maintenance of construction and operation of structures.
- Development and implementation of titanium alloys and methods of surface modification for ship machine-building and heat-exchange equipment.
- Development, research and implementation of titanium alloys for nuclear power units, monitoring of technical state of nuclear power units.
Research and Production Complex "Titanium alloys" performs
R&D and production works according to development strategy of industries for which FSUE CRISM "Prometey" works and based on requirements to parameters of facilities to be manufactured.
R&D
- development of compositions and research of structural titanium alloys with a view to create materials with a required level of physical and mechanical properties;
- modeling of titanium alloy manufacturing processes;
- development of new advanced manufacturing processes in raw material metallurgy, hot and cold plastic working for manufacturing of semi-finished products, heat treatment, welding of structures and creation of welding equipment;
- study of serviceability of base materials and weld joints with definition of guaranteed service life characteristics;
- material science provision of design, manufacturing and repair of equipment and structures of all classes and purposes made from titanium alloys;
- development and implementation of titanium alloys for deep-water facilities, ships, offshore engineering equipment and special-purpose equipment;
- development and implementation of titanium alloys for mechanical engineering and thermal power structures;
- development and implementation of titanium alloys for nuclear power units;
- development of special coatings for surface modification, nanomaterials based on titanium alloys;
- development and release (handing over) of principles of manufacturing process management, manufacturing process and quality inspection of products to manufacturers taking into account operating conditions of produced products;
- expert evaluation of organizational and technical readiness of plants for defined activities, programs, test procedures and inspection of material and facilities state;
- development of engineering estimate procedure and forecasting of strength characteristics of structures made from titanium alloys under influence of damaging factors during the production service.
Production works
Application of functional coatings on surface of parts made from titanium alloys and structural materials in order to increase anti-friction, corrosion resistant, mechanical and electrically-insulating properties.
Tests
- determination of crack resistance of titanium alloys and their weld joints under static and cyclic loads at normal and increased temperatures;
- study of fatigue crack growth kinetics in base metal and areas of weld joint;
- determination of creep rupture strength at high temperatures;
- low-cycle fatigue tests;
- tests and determination of tribotechnical characteristics of friction pairs from different structural materials;
- selection of friction pairs for work under different operation conditions.
Research and Production Complex "Titanium alloys" developed medium-strength and high-strength structural
welding titanium alloys including:
- hull plate;
- alloys for mechanical engineering;
- alloys for energy industry;
Welding titanium alloys have the following advantages:
- high specific strength;
- non-magnetization;
- high corrosion resistance and corrosion and mechanical strength in sea water and in aggressive medium;
- alloys are well welded in homonymous combinations and with other titanium alloys;
- weld joints over a wide range of thickness are equal in strength to base metal;
- large-sized welded structures do not require heat treatment after welding which can cause cold cracks in other materials;
- significant increase of service life of equipment from titanium alloys, reduction of operating expenses and total weight of equipment.
Listed features depends not only on alloy composition but on manufacturing process of semi-finished products and structures.
High specific strength, corrosion resistance in sea water and in other aggressive medium, cold resistance, good weldability, fatigue resistance at high temperatures, low linear expansion coefficient of structures from titanium alloys allow to work under any environmental conditions without life limitation.
Developed titanium alloys for energy industry are marginally subject to irradiation embrittlement. there are practically no radiation induced creep and risk of secondary radiation, induced activity is removed quickly.
Titanium alloys developed by FSUE CRISM "Prometey" are used for manufacturing of critical structures operated in sea water, under extreme conditions and in aggressive medium:
- in shipbuilding - deep-water facilities (including in one-piece titanium version), critical structures, high loaded assemblies and parts of equipment (propulsion systems, steering gears, shafts, bearings) etc.;
- in power plant engineering – heat-exchange equipment (steam generators, condensers), pipe systems (pipes, straight-through valves, valves, damper, filters), piston and centrifugal pump, submersible electric motors and hydraulic drive as well as systems and equipment operated under conditions of neutron exposure for small-sized nuclear power units;
- in oil - gas production - marine engineering production facilities and equipment for transportation of hydrocarbons and other mineral products extracted from ocean soils (including offshore facilities of arctic service), ground and marine pipelines etc.;
- in chemical machine building - for parts and assemblies of equipment operated under extreme conditions (high temperatures and pressure);
- in food industry;
- in medicine etc.
At the present time Russia remains a leader in domain of development of hull titanium alloys and large-sized deformed semi-finished products made from hull titanium alloys for deep-water facilities. In Russia some deep-sea vehicles being as good as foreign equivalent vehicles were manufactured. Hull titanium alloys of FSUE CRISM "Prometey" were used in construction.
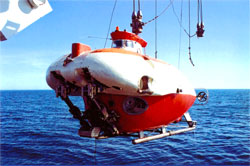
Deep-sea vehicle"Rus"
High reliability of these structures is demonstrated by the fact that a
majority of equipment units were not worn out after long-term operation for
more than 30 years.
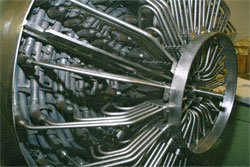
Heat exchanger made from titanium alloy
Use of FSUE CRISM "Prometey" developments is very effective in creation of ground and especially marine equipment for oil-refining and oil-producing industry.
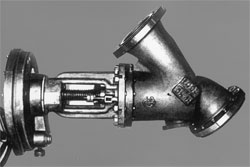
Cranes for oil-refining (oil-producing) equipment
Creation of light titanium fixed and floating drilling oil production platforms for operation in polar regions and northern seas will allow to reduce transportation costs. High reliability of these constructions leads to drastic reduction of operating expenses.
Use of titanium instead of conventional materials is reasonable to increase NPP reliability and efficiency while manufacturing and modernization of process equipment.
Titanium can be also used in design and development of small-sized nuclear power units (weight up to 25 t, power up to 400 kW) which can be delivered by any mode of transport in remote parts of the country for power supply of settlements and mines.
FSUE CRISM "Prometey" developed technical solutions of storage, transportation and disposal of radioactive and toxical products and waste.
It proposed manufacturing technology of pressurized cylindrical vessels for transportation and storage of different radioactive and related substances under any environmental conditions (sea or swamp waters, salt mines, in sea at a depth of 7 km) with leak proof duration more than 500 years. Large above-ground storage-repository can be manufactured in casting and welding version with the same storage life.
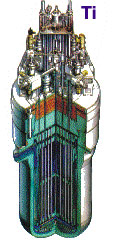
Water-Water Energetic Reactor (VVER) (used titanium alloys)
One of new promising directions of activity is development, research and implementation of low active radiation and corrosion-resistant titanium-based alloys for hull structures of Water-Water Energetic Reactor (VVER) and advanced steam generators of nuclear power plants.
At the XI MOSCOW WORLD SALON OF INNOVATIONS AND INVESTMENTS, (August 26 - 29, 2009, Moscow, All-Russian Exhibition Centre) FSUE CRISM "Prometey" was awarded: Gold medal and diploma for development and technology "Titanium alloy for heat-exchange equipment of nuclear and thermonuclear power engineering".
Mastering of state-of-the-art technologies of semi-finished products manufacturing from these alloys, use of them in energy reactor plant vessels will increase service life of nuclear power unit, environmental safety as well as will ensure quick removal of induced radioactivity and possibility of cheaper disposal of decommissioned equipment.
Use of titanium is also effective for manufacturing of marine and aircraft gas-turbine engines, steam turbines. Problems in vibration and noise control can be solved due to mass reduction of fast moving and unbalanced parts (piston rods, pistons, valves etc.). For this purpose titanium alloy easy-processing by hot forging and having high fatigue resistance and thermal stability were created.
FSUE CRISM "Prometey" developed manufacturing technology of titanium hydrofoil units for dynamically-supported ships of the Kometa and Olimpia types.
Promising direction of titanium alloy use in nuclear power engineering
meeting current market trends are the following:
- manufacturing of semi-finished products for heat-exchange equipment including bimetal titanium-coated sheets;
- manufacturing of hull equipment of nuclear power units;
- manufacturing of turbine plant blades.
As FSUE CRISM "Prometey" inferential research showed the use of titanium alloys equal in strength with hull plates used for manufacturing of nuclear power units can ensure extension of their service life up 60 years and more as well as reduction of radionuclids decay time to 30 years up to safe level and possibility of metal recycling in production.
Considering a perspective of use of titanium materials for manufacturing of hull equipment of nuclear power units firstly it is well to bear in mind experience in development and manufacturing of such equipment by Russian companies namely:
- design of heat exchange and steam-generating equipment from titanium alloys for steam generation plants and smooth-running operation of this equipment in the territory of the Russian Federation;
- design of auxiliary equipment such as the MVZ (metal-water protection) tanks from titanium alloys for medium-power nuclear power units and their manufacturing at Russian plants;
Today there are no foreign analogs of vessels for low- and medium-power nuclear power units and small-sized nuclear power plants of different purpose made from titanium alloys.
FSUE CRISM "Prometey" developed competitive bimetal and functional multi-layer permanent joint of heterogeneous materials using titanium alloys by method of explosive welding with high layer adhesion value due to formation or use of nanostructured states in adhesion area.
At the present time works on development of high-strength titanium alloy for large-sized turbine plant blades of highly economical stationary NPPs are in progress that meets current trends of creation of NPP increased power turbine plants in parallel with significant reduction of capital and operating costs. Solving of this problem will result in improvement of competitive positions of home producers of turbine plants in the world market of power equipment.
Technologies of coating application on titanium part surfaces allowing to increase anti-friction, corrosion resistant, mechanical and electrically-insulating properties were developed.
The 9th
World Conference on Titanium brought international fame to CRISM
"Prometey". This conference was organized and held at high level by our
Institute in 1999 with support of International Materials Research
Societies, Economic Development Ministry of Russian Federation and Ministry
of Science and Technologies of the Russian Federation. More than 500
scientists and specialists from 24 countries of the world participated in
the conference.
Action strategy of Research and Production Complex "Titanium alloys" for the next few years consists in creation of new directions and elaboration of existing directions in development of structural and functional materials, improvement of technology of semi-finished products production, welding technologies and welding materials for manufacturing of titanium alloy structures.
Creation of new direction of ship machine-building – hydraulic system components from titanium alloys operated in sea water and used sea water as a working medium – allows to obtain environmentally friendly equipment with increased service life. To implement such a project it should to develop new compositions of metal-ceramic coatings applied on titanium alloys ensuring practically no wearing of friction pair surface throughout the service life of equipment.
To reinforce a role of structural titanium-based materials it should to develop conception of regulatory documents meeting international standards as well as commitment of designers and manufacturers in innovative projects of national shipbuilding, ship machine-building and nuclear power engineering.
Creation of new directions and development of existing directions of titanium alloys for modern equipment shall be accompanied with training of specialists and scientific manpower of corresponding specialty.